Xiaomi has just presented its first electric car, the SU7, a sedan that is not lacking in interest, just like its production process. Indeed, the Chinese firm seems to have, once again, taken inspiration from Tesla to produce its electric car. Here is the Hyper Casting.
Xiaomi, which has already, in its own way, revolutionized the world of smartphones, is now tackling the car. Its first draft is worth salivating, with the Xiaomi SU7, an electric sedan with quite astonishing technical characteristics, especially for a brand that had never made a car! All the information on the Xiaomi SU7 can be found in our dedicated file.
But apart from its figures, the sedan from the Chinese firm is interesting in more than one way, including its production process which, it goes without saying, strangely reminiscent of solutions developed and used by Tesla ! Xiaomi would not be the first to take inspiration from the American firm on this subject, since Toyota also finds this innovation very interesting.
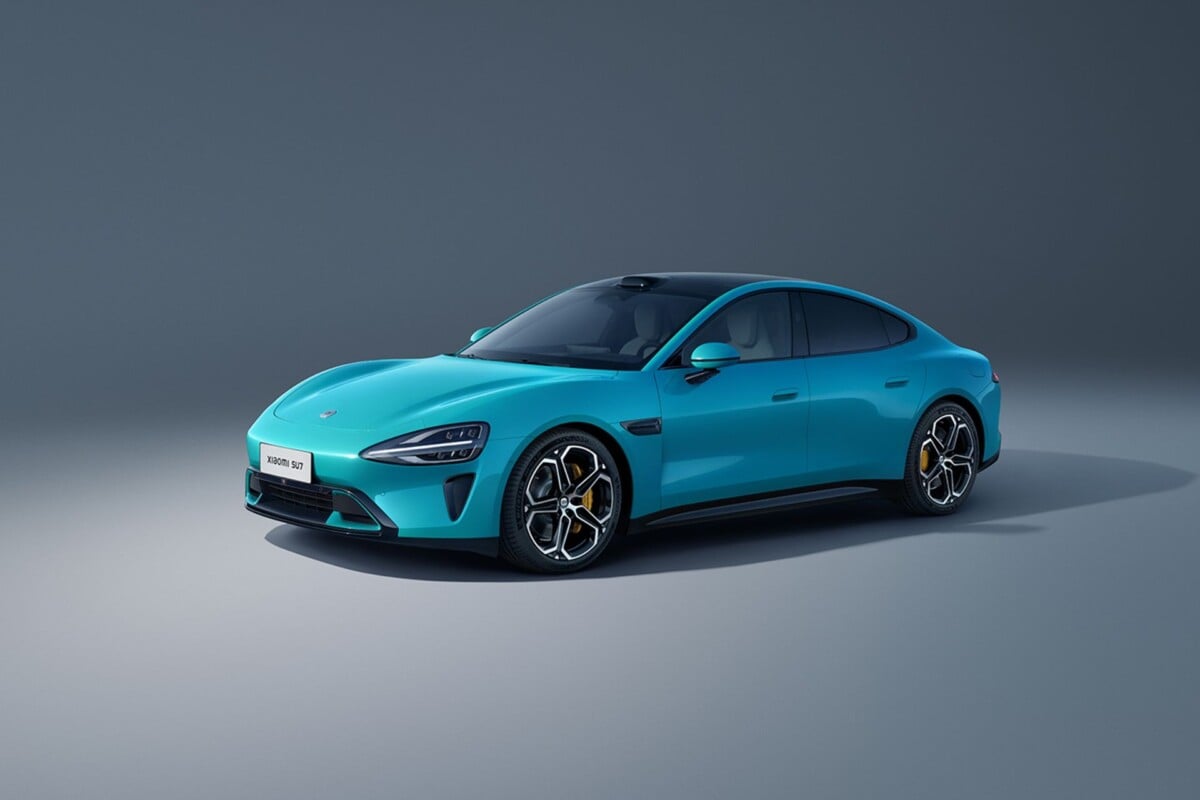
During a recent press conference of Xiaomi Automotive Technology, the automotive division of Xiaomi, CEO Lei Jun highlighted the growing trend of integrated molding in the industry, the same system that became popular with Tesla and its Giga Press. Xiaomi therefore took this route with the launch of its technology Xiaomi Super Large Die Casting (Hyper Casting)“ .
What is Xiaomi Hyper Casting?
A bit like Tesla and its Giga Press, this is a series of die-cast aluminum machines. This obviously allows faster manufacturing, with a more rigid and less heavy structure.
In the case of Tesla, this allows the chassis of a Tesla to be manufactured in three main elements: aluminum alloy front and rear modules, plus central floor. This also makes it possible to eliminate the assembly of at least 370 parts and, above all, it avoids problems with sealing and welding points between the different parts.
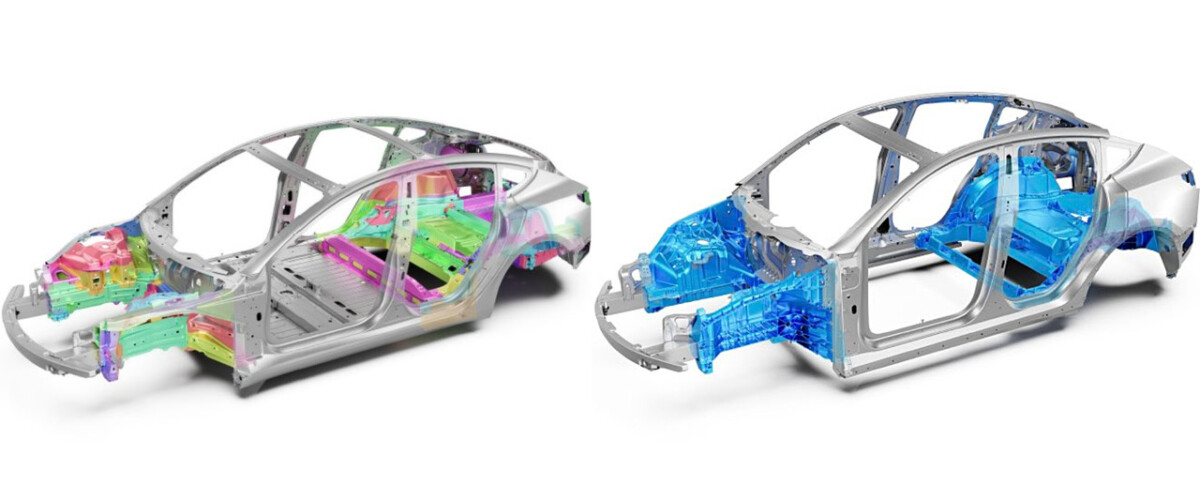
While Tesla uses technology designed by Idra Group, a die-casting machine manufacturer founded in 1946 in Brescia, Italy, Xiaomi simply created its own technology. The Xiaomi Die-Casting T9100 is a massive structure, almost the size of a football field, that is capable of shaping metal with force.
The name of the metal is also in-house, since it is Xiaomi Titans Metal, an alloy created by the company and which, according to it, is stronger and more flexible compared to what is currently used in automotive production. By using and combining these two elements, Xiaomi claims that the SU7 integrates 72 components into one for its rear underbody, improves the noise reduction inside the vehicle by 2 dB, the welded joints are only 840, the weight of the car is reduced by 17% and this saves 45% of production hours.
This new molding system benefits with a force of 9,100 tonnes, surpassing Tesla’s Giga Press in the United States by a hundred tons. Installed in Xiaomi’s automobile factory in Beijing, this equipment weighs 1,050 tons and occupies an area of 840 square meters.
An already well-oiled production system?
To ensure absolute reliability, Xiaomi has developed a very precise process. Xiaomi Die-Casting integrates multiple molding units, each with a capacity of 9,100 tons, working in a coordinated manner. A system automatically manages the transport of molten aluminum in a sealed environment to avoid contamination and ensure consistent quality, all the way to the molds.
In a mold, there are five precise zones and eight entrances for pouring the aluminum, “for optimized flow and filling of molten material”, according to Xiaomi. Once the part is molded, a system that uses visual analysis, likely through cameras or sensors, is responsible for evaluating the quality of the molded parts. These same parts then pass through a platform designed to test the durability of the products.
Once tested, these elements go to a platform that allows the safety of molded products to be evaluated under compressive stresses.
What are, in concrete terms, the advantages of such a production process?
This system allows simpler, faster and more efficient production. From a technical point of view, on a car, this changes quite a few things. Fewer parts also mean less weight. Less weight is also decreasing consumptiontherefore an increased autonomy and, consequently, this does not require the addition of new battery cells to increase the autonomy.
You may have noticed, but traditional manufacturers are not rushing to adopt this system, apart from Volvo (under the leadership of the Chinese Geely, and Toyota).
But why ? This type of technology requires a fairly colossal investment in terms of engineering, in particular to develop cars adapted to this production system, and with the synergies between the different brands of the different groups, it is much more than a simple factory or than a simple structure that should be reviewed, but almost an entire range and production process.
An infallible system?
And that’s not the only problem. Several questions arise regarding this production process, for example, the type of repair to be carried out on the chassis in the event of a vehicle accident.
Indeed, by reducing the number of parts, this gives us several large parts, more exposed, and therefore more expensive to replace (if possible!) rather than several “small” parts to replace in the event of a minor incident. But, like Tesla, the Xiaomi factory has undoubtedly been thought of differently and brings together practically the entire production process within the same establishment.
This is not the case for large groups, where sometimes this or that part is made in this or that place, in several different factories, to then be assembled again in another factory. If manufacturers do not centralize their production process, then transport costs will literally explode.
However, let us also point out that we are at the beginning of these famous Giga Presses. Manufacturers generally do not yet have enough perspective to know with certainty whether these machines have, in the long term, a good rate of return, and whether their maintenance is also easily manageable.
This production process mainly aims to save money in this sector, this will undoubtedly be beneficial for customers. As for Tesla, the future Tesla Model 2 will benefit from this manufacturing process to bring prices down, and reach the $25,000 promised by Elon Musk.
At Xiaomi, we do not yet know the prices of the SU7 (or almost), but this production system should above all benefit other models that we can’t wait to discover!