Frandroid was invited to Saint-Quentin, in Aisne (02), to visit the newly named Yamaha Motor Manufacturing Europe SAS which historically manufactures thermal scooters. Recently, a brand new production line dedicated to the design of motors for electric bicycles has taken shape. Operation, safety and speed: alongside us, dive into the bowels of the machine.
Last January, the company that was formerly called MBK Industrie SAS experienced a highly symbolic change by abandoning its surname with that of Yamaha Motor Manufacturing Europe SAS Descendant of Motobécane – which came under the fold of the Japanese giant in 1986 -, this French factory located in Saint-Quentin, in Aisne (02), has decided to embrace the great trend of our era, that of electricity.
Historically, the factory is the place for the design of well-known thermal scooters and motorcycles: the Ténéré 700 and MT-125 motorcycles for example, but also the best-seller of the Japanese brand, the famous XMAX. In the year 2024, the group is adjusting its focus by setting up a brand new production line dedicated to electric bike motors.
A sister line from Japan
In reality, only one engine is currently produced: the PW-S2, launched in September 2022. This is a Japanese twin line, directly “imported” from the parent company with “more advanced security adjustments », in order to comply with European standards, explains a representative of Yamaha France.
To deploy it, “we went to Japan, we had maintenance, quality and development training», Explains our interlocutor. In the future, other engines can be produced on this production line, which is compatible with other systems and inspection benches.
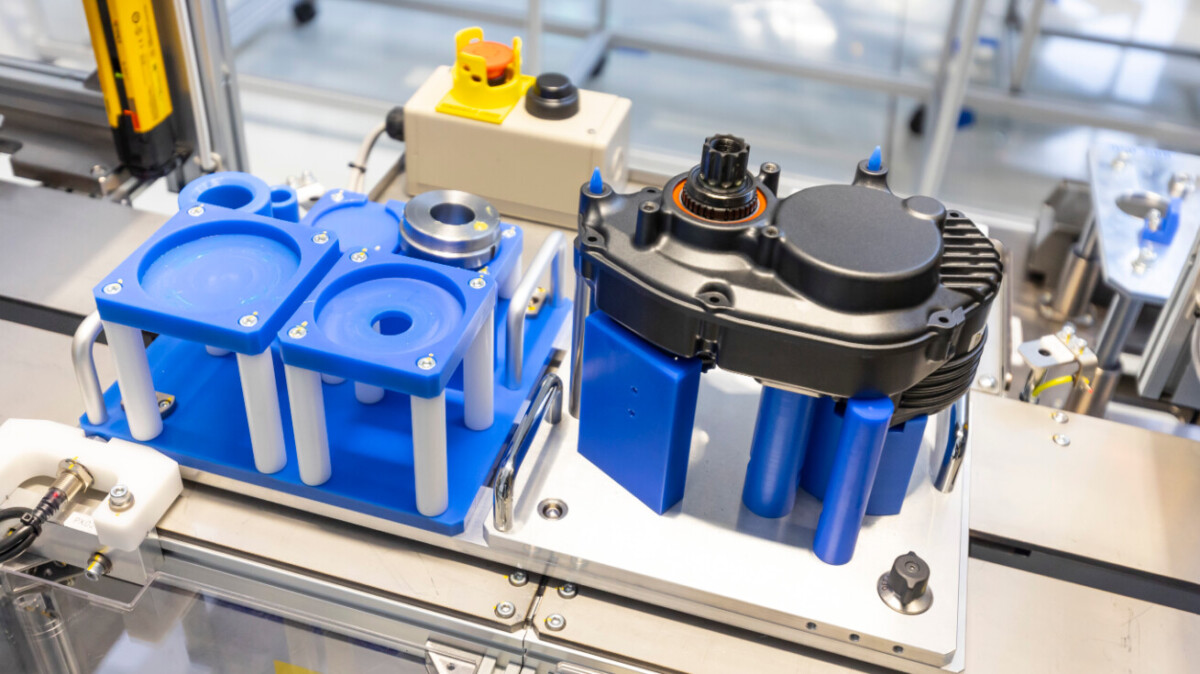
More concretely, how does this famous line work? The parts are first organized by trolley then taken to a so-called preparation line. Here, subassemblies made up of parts are assembled on dynamic racks by operators. “These are the gears, the bearings, we prepare the mechanics of the motor before assembling them», we are told.
This little merry-go-round allows you to create kits and validate the presence of all the assembled parts. Everything then goes to a conveyor line made up of 6 work stations. “We have keyers which validate each operation, to know if everything is designed in the right order, with the right parameters, and to authorize movement towards the next operation“.
Checks, anytime and anywhere
Yamaha makes a point of checking literally everything, to minimize the margins of error. “The work is 100% manual, the machine is mainly there to control“. This is the group’s policy, which applies the same methods in Japan and France.
During the process, parts and subassemblies are demagnetized, “because there may be static electricity» which some systems do not appreciate. This can particularly impact the torque sensor, which needs to be cut off from the magnetic field otherwise it may become non-functional.
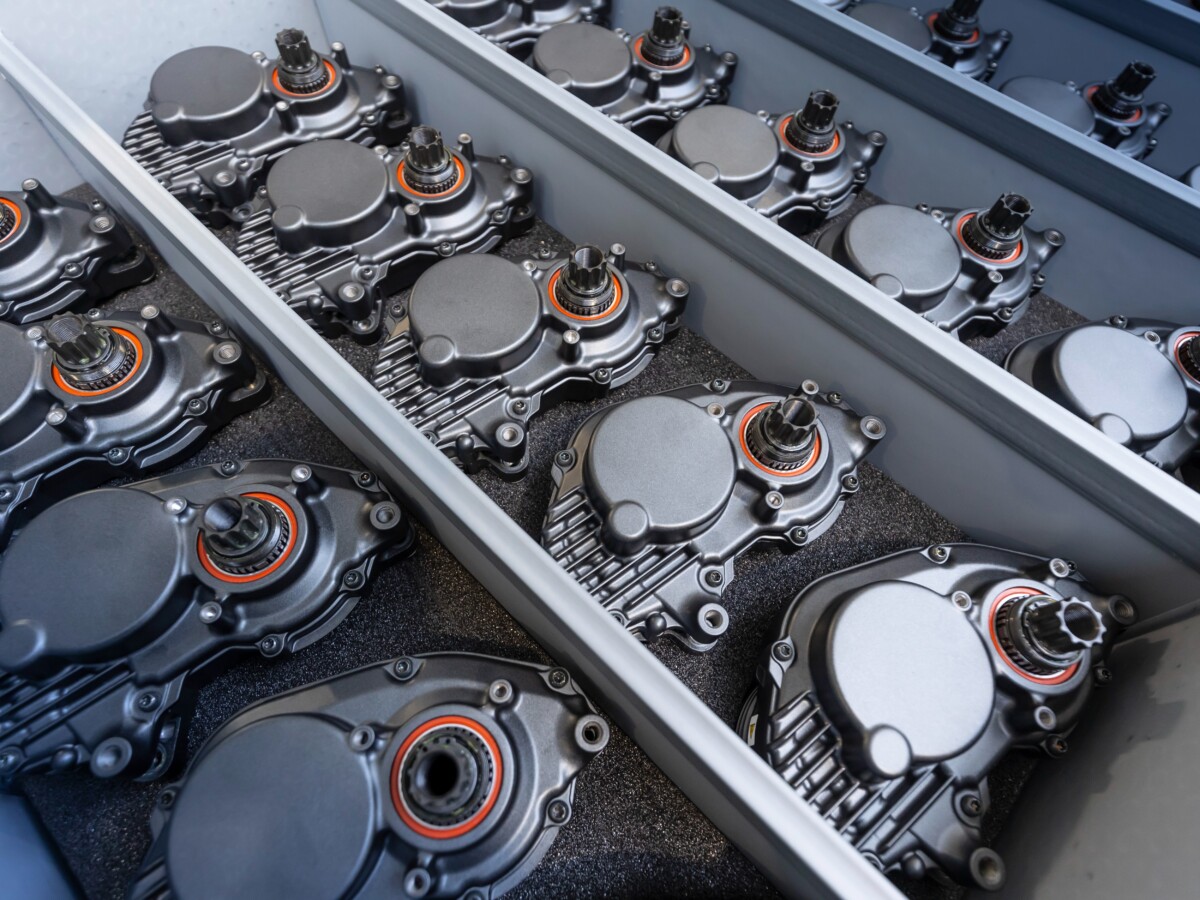
Ultimately, a robotic system is responsible for applying seals to ensure the engine is watertight. Yet another camera check, this time checking the entire engine with imaging. Yamaha preferred to remain discreet about the number of checks carried out. “What is necessary”, we were simply told.
Finally, the motor is subjected to an inspection bench: here, a machine will enter the motor parameters to control its quality, calibrate it, understand at what angle it is working and validate the performance. This is a very strict and in-depth control, which also allows the product to be traced down to the smallest detail.
Safety stocks
The final step is to install the motor housing, which is then stored in a rack with a again controlled drying time – just under half an hour. The first engine part produced is the first to be used, to respect drying times. Once the engine is finished, it is shipped in returnable boxes that go back and forth between Yamaha and the customer.
In the event of a problem with a part, the Japanese firm identifies it, changes it and records it to know which batch it comes from. Not surprisingly, Yamaha has a safety stock to overcome this type of problem. More generally, the group ensures a stock of engines so as not to have any constraints vis-à-vis a customer, even if it means having a bit of overstocking.
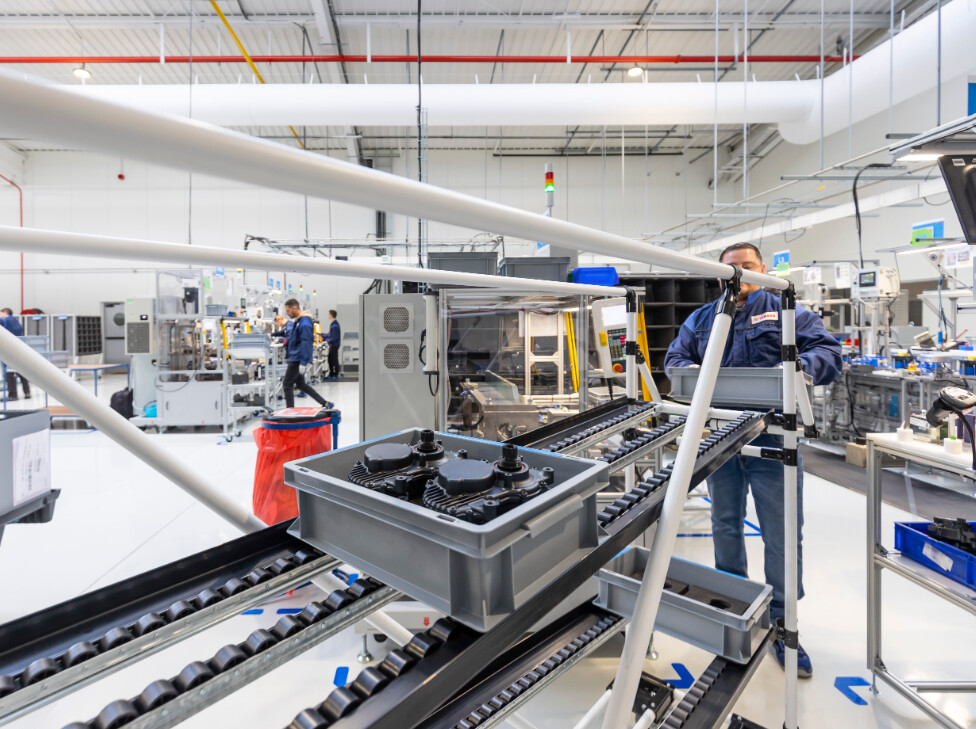
In total, each engine has around 60 parts, with several subassemblies sent directly from Japan. This production line calls on around fifteen operators at all times: each of them can hold all the positions (one position requires one day of training), we are assured. This allows them to develop their versatility, avoid muscular disorders due to a single task and increase their skills.
A motor every minute
A team of 15 people manages to release an engine every minute. From its start on the production line to the very end, a motor takes approximately 20 minutes to be designed. In total, the factory is able to produce 100,000 engines per year, per shift, if the line runs 24 hours a day. Ultimately, Yamaha wants to add two additional shifts.
Within a few days – article written on March 29 – a first batch of motors will be delivered to the customer in a truck containing… 4,500 motor units. Yamaha’s main customer is also well known: it is Accell Group (Winora, Babboe, Haybike, Lapierre), number 1 in bicycles in Europe which is currently going through a deep crisis (debt, relocation, technical problem and reminders).