The galloping electrification of the automotive sector is reshuffling many cards, even going so far as to modify car manufacturing methods. Invented by Tesla, taken over by the Chinese & Toyota, “mega casting” promises savings, speed, scalability and lightness for electric cars. Volvo will be the next manufacturer to implement this technique, and we went to see this gigantic press in its environment, in the brand’s historic factory in Sweden.
With their gigantic batteries in their floors, electric cars open up unexplored avenues with thermal vehicles in many areas. Whether in terms of architecture, maximization of living space or distribution of technical components, this new way of thinking about a car’s chassis opens up the field of possibilities.
Tesla understands this well and has completely revolutionized the way cars are manufactured with its Model Y. At the forefront: “giga casting”, which allows gigantic parts to be molded in one go. A clearly brilliant idea, since Xiaomi used it for its first electric car, the SU7, and even Toyota is considering implementing it.
Latest manufacturer to date: Volvo, for its next 100% electric model planned for 2025. We went to see this brand new press in the brand’s historic factory, in Sweden, in the suburbs of Gothenburg. Here are all the secrets of this new technique which promises wonders.
“Mega casting”: instructions for use
Volvo, like almost all car manufacturers selling in Europe, will become a 100% electric brand – and this, from 2030. To gain competitiveness compared to thermal models and Chinese brands (eagerly launched into a bloodthirsty ” price war”), Volvo must innovate.
One of the major levers for the industry therefore seems to be this famous “mega casting”. The idea is simple: if a car floor is usually an assembly of a multitude of small parts welded together, this process makes it possible to manufacture entire parts in one go.
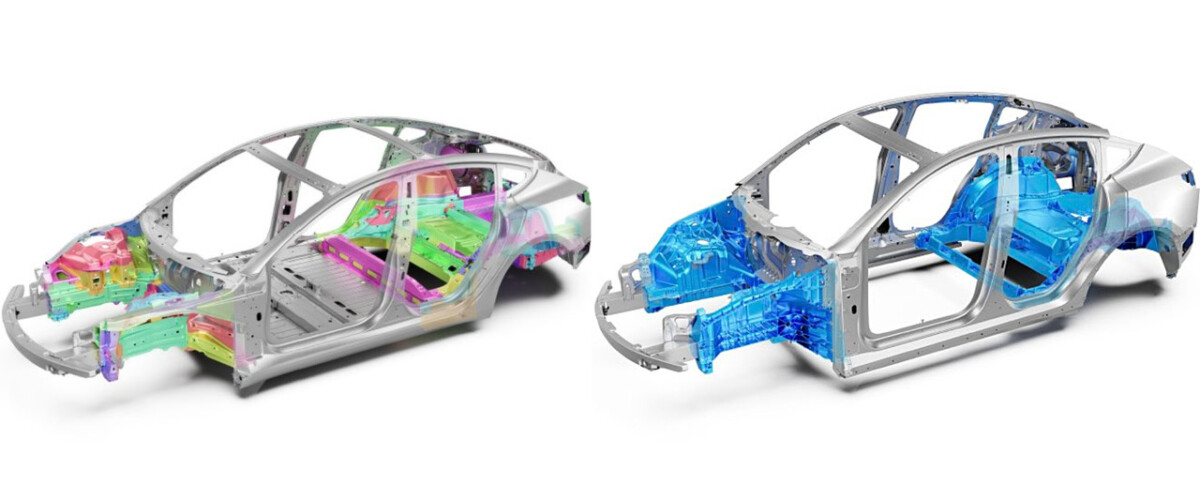
Very concretely, the part in question, the rear floor, will thus go from an assembly of 100 parts to a single block. At Tesla, as we can see in the image above, we are going from 171 to 2 different parts. At Volvo, this starts with the aluminum ingots, which will be melted at 730°C, then purified, before passing through the famous “giga press”. At this moment, a force of 8,400 tonnes is exerted on the liquid aluminum, enough to form the raw part.
This part will then be cut to fit the car perfectly, and the scraps will be immediately recast for the following parts. It’s then time for machining, then a final quality test before joining the assembly line.
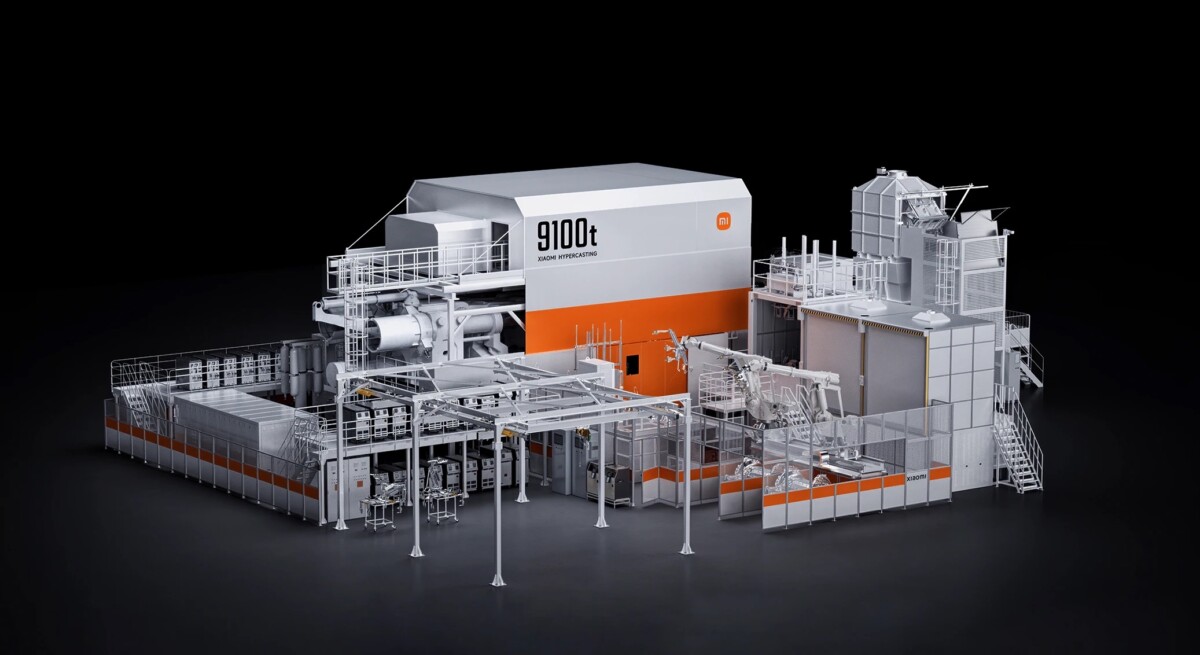
Rhythm ? One piece every two minutes, five days a week, 24 hours a day. Volvo ultimately hopes to produce 300,000 parts per year. If one press is already operational in Torslanda in a brand new building, a second is being assembled, and space is planned for a third.
What are the advantages?
Lots of positives…
A mega casting (also called “giga casting” at Tesla or “hyper casting” at Xiaomi, you will note the semantic efforts) which only has advantages, if we are to believe Mikael Fermér, the lead architect for vehicle platform at Volvo.
On the vehicle side, this allows several things:
- a weight saving thanks to the absence of welds and the use of aluminum instead of steel: Volvo announces a weight reduction of 15 to 20%. And a decreasing weight means a decreasing consumption, and therefore an increasing autonomy;
- constant scalability: instead of reindustrializing all the molds and creating a whole new process for each new technology (a new rear axle or an additional electric motor, for example), it “is enough” to change the shape of the part , a process that is a priori much quicker and more economical to implement.
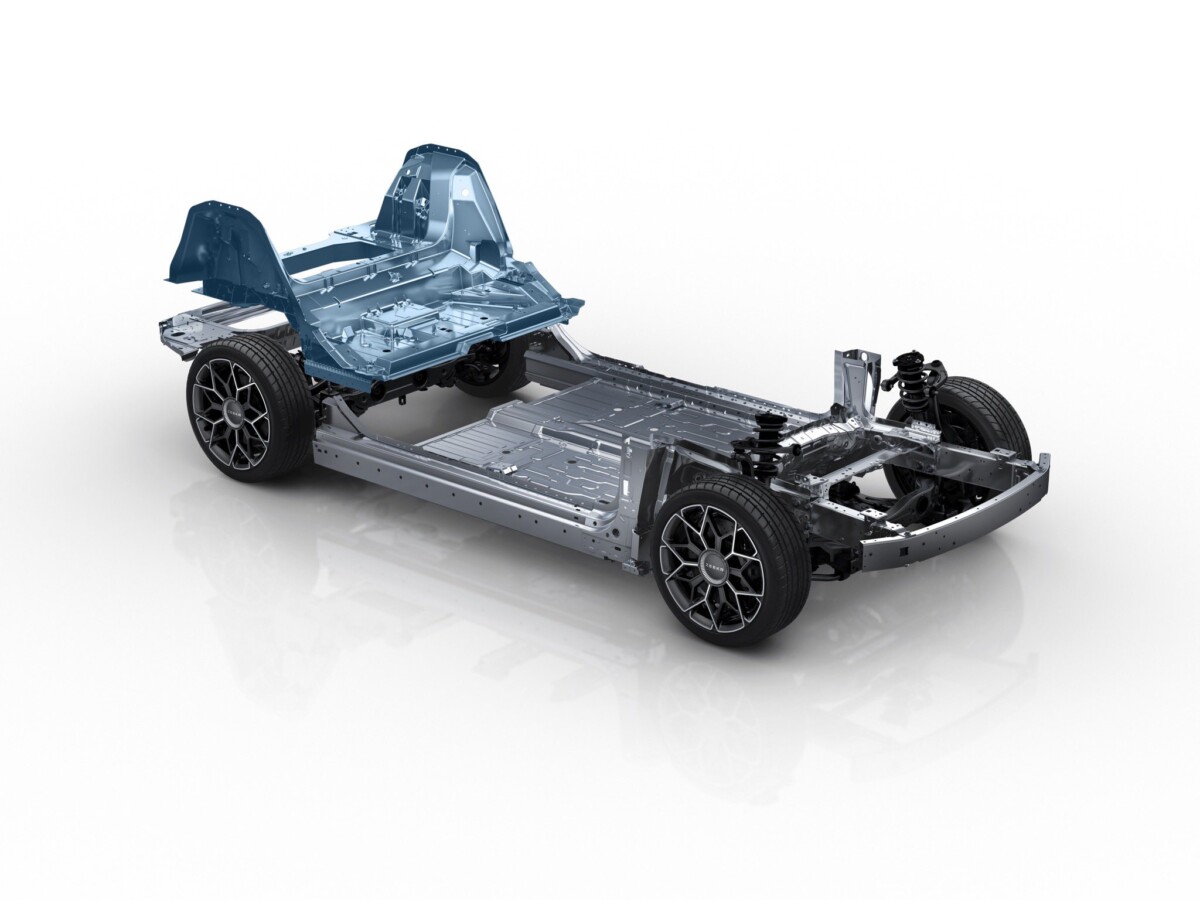
It doesn’t stop there, as Torlsanda plant manager Magnus Olsson adds these additional points:
- Logistics is a crucial point for the proper functioning of a factory (and therefore for the quality and regularity of assembly lines). On this point, mega casting makes it possible to internalize the entire process, otherwise dispersed among a multitude of service providers. The key: saving time, saving money, gaining control, all benefits.
- in addition, mega casting makes it possible to reduce the complexity of industrialization: instead of a multitude of robots welding small parts together, the entire process is managed by a single machine.
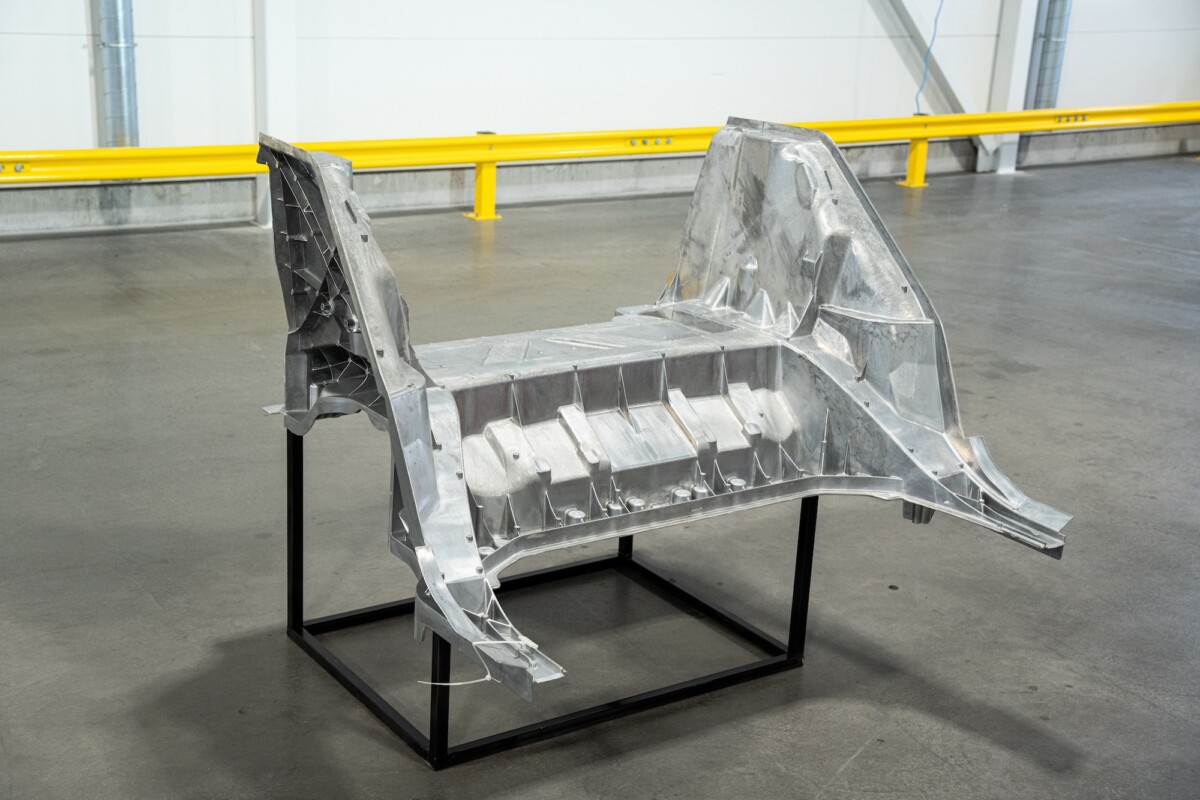
Finally, the environmental aspect is also highlighted:
- internalizing the process makes it possible to avoid transport between suppliers and the factory;
- material losses are much lower than with a welding technique: Volvo estimates that 50% of the base material is lost with the traditional technique; for giga casting, this figure will drop drastically, even more so with the immediate reuse of scraps;
- generally, a policy of increasing the share of “secondary aluminum” (read “recycled”) is put in place. Count on 20% at the beginning, then 30% in the medium term, with an optimal of 50%.
…but some negative points
A cascade of compliments, therefore, but which should not make us forget that the mega/giga/hyper casting does not only have qualities.
Mikael Fermér recognizes this without any problem: in the event of an accident, a part resulting from this process will not be optimal (and safety, for Volvo, is important). On the one hand because its deformation performances do not reach those of traditional parts, but also because the repairability of a “mega cast” part is complicated.
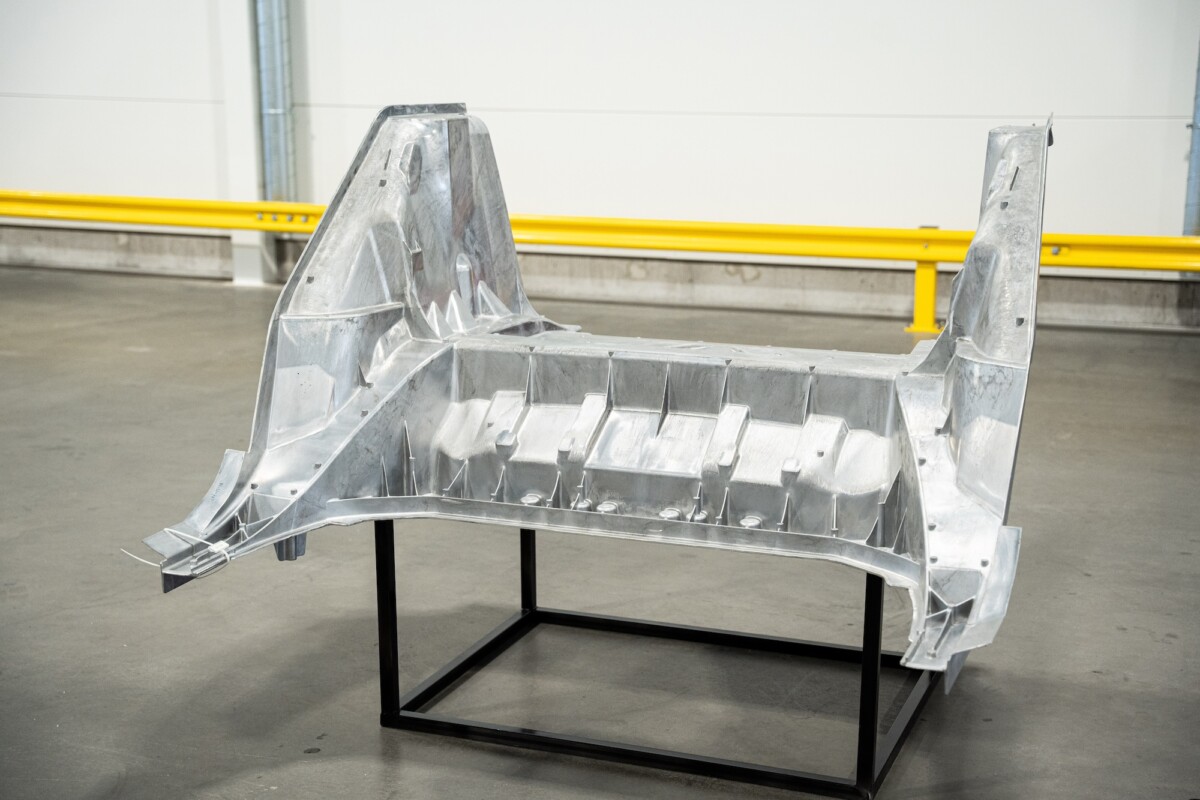
This is a point that we are already starting to see with Tesla, but a car with such a part damaged will have a greater chance of ending up in the scrapyard. Faced with these two problems, Mr. Fermér wants to remain optimistic, and explains to us that a deformation zone is planned between the bumper and the part itself.
This allows maximum energy to be absorbed in the most optimal way possible, while keeping the “giga cast” part intact. Thanks to this, he hopes that the insurance premiums will be the same as those of a “traditionally” manufactured car.
For its part, Tesla has set up an independent working group external to the company to find out whether giga casting complicates repairs in the event of an accident.
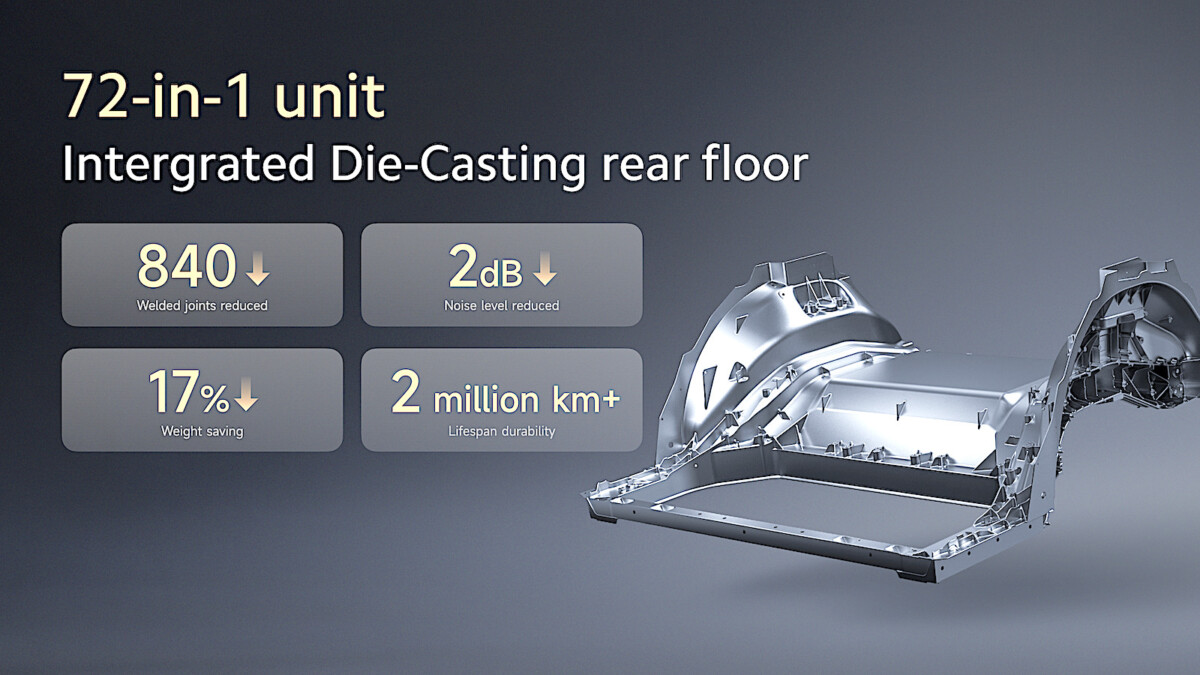
Asked about the future of the staff currently dedicated to welding activities, Magnus Olsson wants to be reassuring, and promises that all the workers (and workers, who represent 30% of the factory’s payroll!) will be trained to work on giga presses or on another activity.
One billion euros for the historic factory
These three presses are part of Volvo’s significant investment (via Geely, owner of the brand, as well as Lotus and smart) to prepare the Torslanda site for the total electrification of the range.
In addition to the mega casting, a battery production factory (the famous gigafactoryanother term familiarized by Tesla) is also planned in a joint venture with Northvolt, one of the major European battery players.
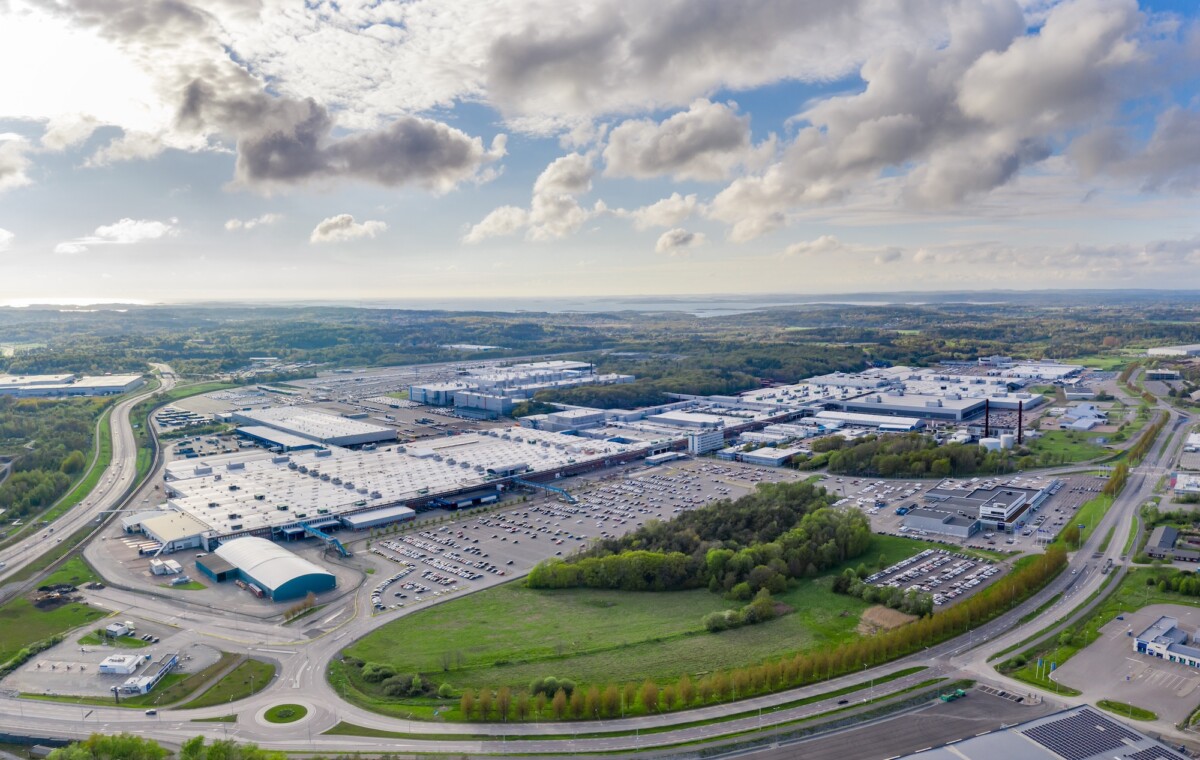
The latter, located 500 meters from the production line, will directly supply the battery cells which will arrive in the electric Volvos assembled on the site. “A good way to further reduce the costs and carbon footprint of our cars”approves Magnus Olsson.
This gigafactory will produce its first series cells in 2026, one year after the start of production of Volvo’s next electric car, which will be the first to use the “mega cast” rear floor.
A model that is still very mysterious, since the well-locked communication has not allowed us to discover anything about it. Neither the format (although we assume it will be an SUV the size of the current XC60, which could be called EX60), nor the battery chemistry (NMC? LFP? Both?), nor the autonomy, nor prices, nothing. You will have to be patient.