CO2-speiende Fabriken, die die globale Erwärmung anheizen, könnten der Vergangenheit angehören, wenn Hersteller die neueste digitale Technologie einsetzen, um die CO2-Emissionen zu senken und die Energieeffizienz zu steigern.
Die verarbeitende Industrie ist für fast ein Viertel der weltweiten CO2-Emissionen verantwortlich und muss ihre Verhaltensweisen ändern oder die Verantwortung für den Beitrag zum katastrophalen Klimawandel tragen, so die neueste Bericht vom Weltklimarat der Vereinten Nationen (IPCC). Während das Gremium die Hersteller dazu drängt, neue, nachhaltige Produktionsprozesse einzuführen, wenden sich Unternehmen fortschrittlicher digitaler Technologie zu, um die CO2-Emissionen zu senken.
Eine Reihe von Technologien, die als vierte industrielle Revolution bekannt sind – darunter Systeme wie Robotik, künstliche Intelligenz (KI), dezentrales Edge-Computing und Datentrendüberwachung – trägt dazu bei, Fabriken effizienter und nachhaltiger zu machen.
„Was uns diese Technologie der vierten industriellen Revolution bietet, sind sehr detaillierte Daten, die zu größerer globaler Transparenz und Sichtbarkeit führen“, sagt Johannes Holtbrügge, Senior Manager für digitale Transformation bei Henkel, einem globalen Hersteller von Klebstofftechnologien und Konsumgütern. „Das ermöglicht einem Unternehmen wie unserem, zu verstehen, wo wir den Energieverbrauch senken können, und Wege zu finden, um Abfall und übermäßigen Wasserverbrauch zu reduzieren, was uns hilft, einen positiven Einfluss auf die Umwelt zu haben“, sagt er.
Der Geschäftsbereich Laundry and Home Care von Henkel stellt Waschmittelmarken wie Bloo, Color Catcher, Dylong und Jeyes her, und das Unternehmen setzt auf die neue Technologie, um alle CO2-Emissionen aus seinen Produktionsprozessen zu entfernen und bis 2030 ein klimafreundliches Unternehmen zu werden – d.h. überschüssige CO2-frei produzierte Energie kann von Dritten genutzt werden.
Ab 2013 begann Henkel damit, Tausende von Sensoren in seinen 30 Wasch- und Reinigungsmittelfabriken weltweit zu installieren, die alles vom Stromverbrauch bis zum Wasserdruck in Echtzeit messen. „Dies hat uns Transparenz und Einblick gebracht und es uns ermöglicht, Fabriken zu bewerten und zu vergleichen, damit sie voneinander lernen können. Die clevere Nutzung dieser Daten hat uns geholfen, unseren Energieverbrauch zu reduzieren und Abfall zu reduzieren“, sagt Holtbrügge.
Früher wurde der Energieverbrauch gemessen, indem ein Techniker zum Ablesen des Zählers geschickt wurde. Mit dem Sensornetzwerk ist ein kontinuierlicher Datenfluss über den Energieverbrauch, den Wasserverbrauch und die Gasversorgung von Fabriken in den USA, Nordamerika, Asien, Afrika und Europa verfügbar. Diese Daten können beispielsweise kombiniert und analysiert werden, um zu zeigen, wie Druckluft, die Maschinen antreibt, effizient genutzt und verteilt werden kann. Oder wenn die Sensoren die Ingenieure auf einen plötzlichen Abfall des Wasserdrucks aufmerksam machen, deutet dies darauf hin, dass irgendwo ein Leck sein muss. Die schnelle Ortung von Lecks reduziert den Wasserverbrauch. Vor den Sensoren hätte es Tage dauern können, bis man merkte, dass ein Fehler vorlag.
Unterdessen zahlt sich die digitale Vernetzung von Fabrikarbeitern auch für die Umwelt aus. Sicherheitsinspektionen in den Fabriken werden von Mitarbeitern durchgeführt, die mit iPads ausgestattet sind, mit denen sie Auffälligkeiten in einer App erfassen und mit Fotos dokumentieren können. Früher wurden Inspektionen auf Papier festgehalten. Rund 200.000 Werksbegehungen wurden mit diesem vernetzten Arbeitersystem durchgeführt und sie haben die Werkssicherheit verbessert und erhebliche Ressourcen eingespart.
Diese Initiativen haben Henkel dabei geholfen, erhebliche Einsparungen beim Energieverbrauch zu erzielen, und haben das Unternehmen fest auf den Weg gebracht, seine klimapositiven Ziele für 2030 zu erreichen. Seit 2011 hat das Unternehmen 16 % bis 18 % Energie eingespart, indem es diese digitalen Fähigkeiten zusammen mit anderen Effizienzeinsparungen nutzt. Etwa 3,5 Millionen Tonnen CO2 wurden in den letzten 15 Jahren aus dem Produktionsprozess entfernt, wodurch jährlich etwa 10 Millionen Euro (8,5 Millionen Pfund) an Energiekosten eingespart wurden, sagt das Unternehmen.
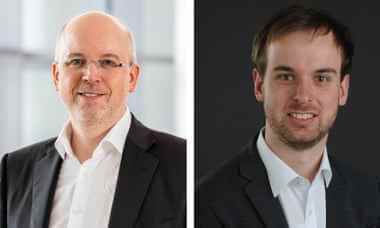
Dirk Holbach, Corporate Senior Vice President und Chief Supply Chain Officer bei Henkel Beauty Care und Laundry & Home Care, sagt, dass die vier Hauptbereiche der Technologie der vierten industriellen Revolution bei Henkel – Robotik, Sensoren, Analytik und Visualisierung – zusammenwachsen. Die von den Sensoren erzeugten Daten werden analysiert, oft unter Verwendung von KI-Algorithmen, und dann durch Visualisierung in leicht lesbaren Grafiken auf einem Dashboard dargestellt. Roboter, die verwendet werden, um Produkte für den Versand auf Paletten zu heben, verwenden sowohl Sensoren als auch Analysen, um ihre Aufgaben zu erfüllen. „Die wirklichen Vorteile des vierten Industriezeitalters werden realisiert, wenn diese Technologien alle zusammenwirken“, sagt Holbach.
Dies wird enorme Auswirkungen auf die Lieferketten haben – die Produktions- und Logistikbasis von Industrie- und Verbraucherunternehmen. Lieferketten tragen bis zu 90 % der weltweiten CO2-Emissionen vieler Unternehmen und die derzeit getestete Technologie trägt dazu bei, Emissionen zu reduzieren und gleichzeitig eine neue Art von Lieferkette zu schaffen.
In den letzten Jahrzehnten hat die Industrie versucht, schlanke und effiziente Lieferketten zu schaffen, die die Lagerbestände minimieren und zu einem Just-in-Time-System beitragen, bei dem Durchhang aus der Kette entfernt wird. Dieser Ansatz ist in letzter Zeit unter Druck geraten, da er während der Pandemie und ihrer Folgen Probleme hatte. Angesichts der Kombination aus dem Wettlauf um CO2-Null, der Technologie der vierten industriellen Revolution und den Lehren aus der Pandemie besteht ein Bedarf an besserer Notfallplanung und kontinuierlicher Verbesserung.
Für Holbach bedeutet der neue Ansatz, weg von schlanken Lieferketten hin zu dem, was er die „bewusste Lieferkette“ nennt.
„Du brauchst Sensoren, du brauchst Daten, du brauchst Modelle, die deine Aktivitäten repräsentieren, und dann musst du bewusst telefonieren“, sagt Holbach. „Man muss darauf achten, welche Art von Entscheidungen man trifft, aber das bedeutet nicht jeden Tag denselben Anruf, da sich die Situation immer sehr dynamisch ändert. Man muss bei jeder Entscheidung, die man trifft, wachsam sein.“
Während frühere industrielle Revolutionen die Produktivität gesteigert haben, ohne an die umfassenderen ökologischen und sozialen Auswirkungen zu denken, gibt es große Hoffnungen, dass das vierte industrielle Zeitalter diese Überlegungen ganz oben auf die Tagesordnung setzen wird.
Finde mehr heraus darüber, wie Henkel digitale Technologien nutzt und sein Know-how einsetzt, um die Transformation zu Industrie 4.0 voranzutreiben